I am playing catch-up with many things including getting everyone up to speed on my progress with Rock Creek trestle model. Unlike many folks, COVID was not a super-duper productive time for me with my model railroad. At the outset of the stay-home orders, I embarked on a remodeling project that took most of my time, sanity and family peace away for several months. The upstairs guest (kids) bathroom was gutted and renovated all by myself. This included a completely new tub, surround with tile, plumbing, new tile flooring, toilet, vanity/sink, beadboard, ceiling fan, and a custom-made mirror made using the very large old one and some leftover trim. It all came together in the end, but the journey burned me out. I found that I had no time during the project to work on my model railroad, and for a very long time after was uninterested in doing layout work at all. As such, my progress over the last year has been slow.
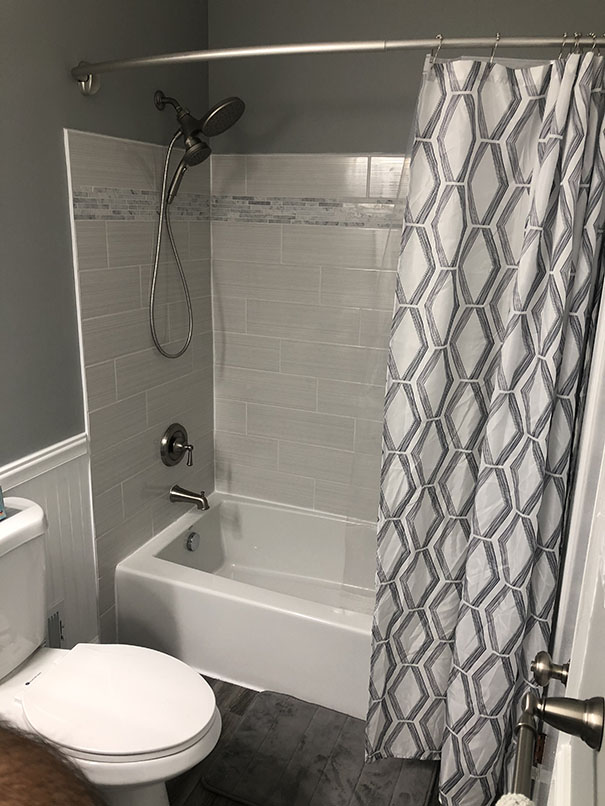
NONETHELESS, I have made progress! Today I’m going to share a slew of photos showing where I am with the Rock Creek trestle model. This will be a showcase piece on the layout so taking my time is not necessarily a bad thing. I’m learning A LOT along the way with this scratch build and it’s been fun so far. Tedious, but fun. If you recall from previous blog posts, I drew the plans from drawings, photos and some measurements I made. The challenge was great, as there are no good reference photos from the time frame I want to model (late 1940s) so a lot of time was spent making careful judgements and measurements from the few photos I DO have. In the end, I’m quite proud of the plans I made.
I started in earnest on actually building the trestle back in June of 2020. (yeah, yeah, a YEAR AGO…) A few early experiments helped me to refine my technique for how to assemble the trestle bents. At first I had hoped to use a magnetic tray to lay out the parts. This quickly was dismissed, as I realized the magnets did not allow for fine adjustment and placement that was necessary for this sort of construction.
Reaching back to my youth, I decided to use the same technique I used to build balsa airplanes; pins. This turned out to be a great choice, and paired with small slabs of 2″ extruded pink foam boards, worked beautifully.
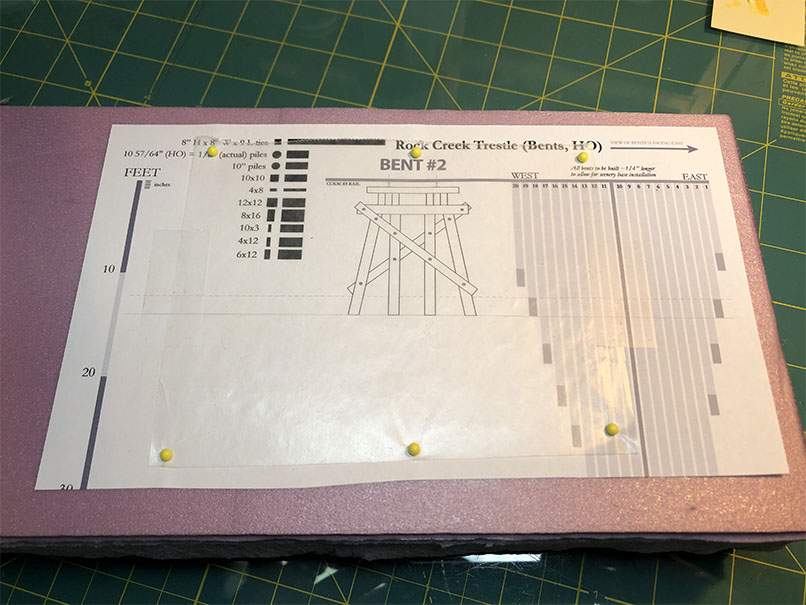
My technique is to trim the 8.5×11″ sheet of paper the plan is printed on to fit on the foam block. Then, place the plan down and a small sheet of wax paper atop it. Use pins to secure to foam. Then I will place my dimensional lumber atop the plan to mark and cut using The Chopper II or a new X-Acto blade. I use the NWSL True Sander to achieve a good angle on the trestle bents. I use white glue (used carpenter’s glue for a while) and pins to hold the pieces in place while they dry.
The benefit of using the slabs of pink foam is that I can have 5-6 of them working at once. I start one, glue and pin it up, then set it aside. Prep another bent, glue and pin it, set aside. Rinse and repeat. Once a bent is dry, I flip it over and finish the other side. I made up an angle template for my Chopper to cut bents at a consistent angle. I would then clean them up on the True Sander. These were really coming together nicely.
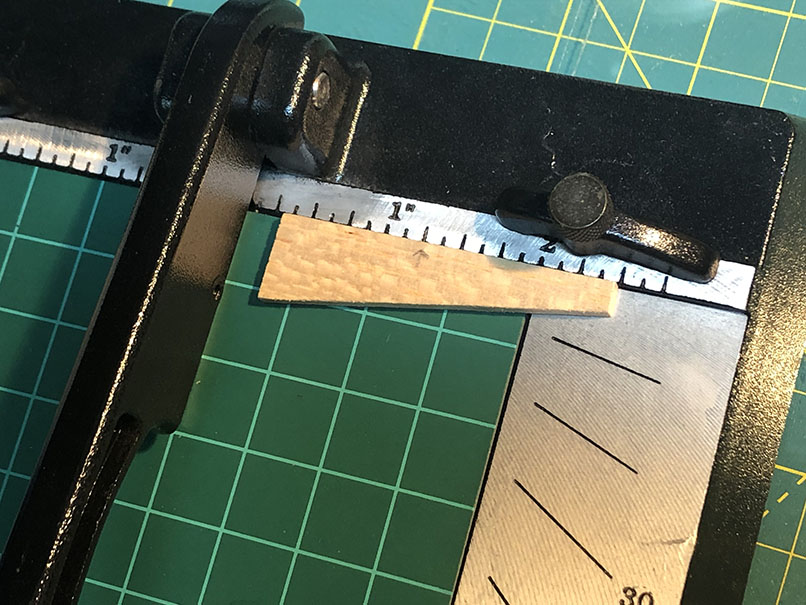
After the bents had dried, I would trim up any angles or edges with an X-Acto blade. The next step is to install the NBW (Nut-Bolt-Washer) castings. I prefer the Tichy 8016 as they are molded in brown plastic and reasonably well resemble the prototype. I also have some of the NWSL 5046 NBW and they are very nice, too. EDITORS NOTE: While writing this, I looked more closely at the image below and realized I should be using the NWSL 5066 (1 1/4″ NUT, 3″ MALLEABLE WASHER .014″), as it is a MUCH better match. I will have to get some of these now.
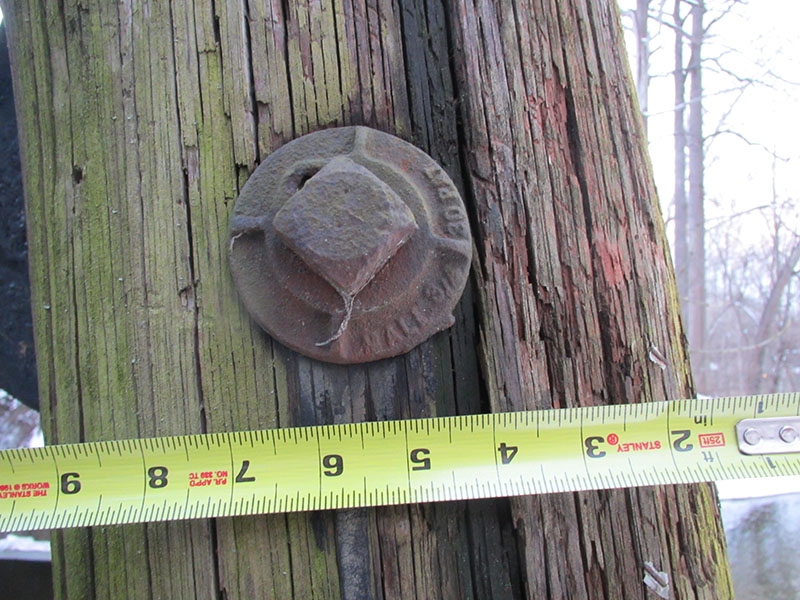
I first painted the tips a rust color, trimmed using sprue cutters and then installed the NBW castings on several bents using a pin vise and a small #76 drill.
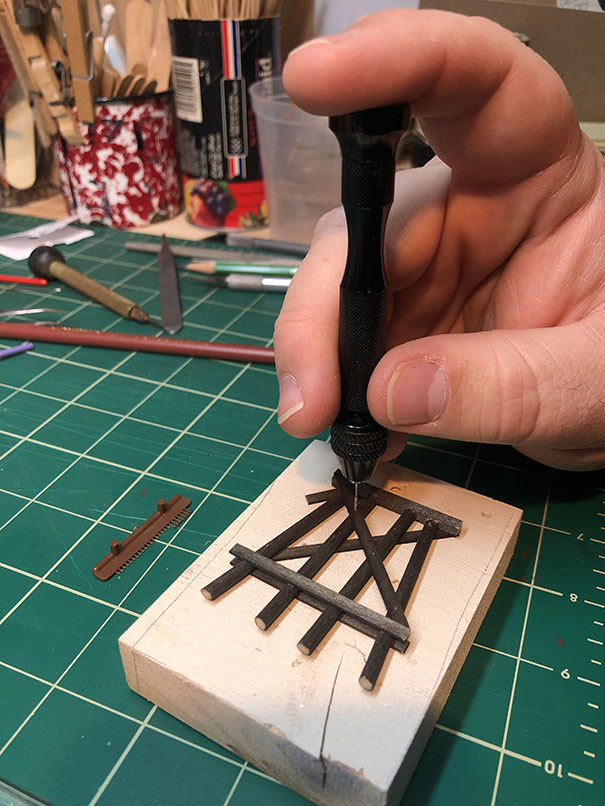
The results were quite nice, but my fingers were starting to get really sore.
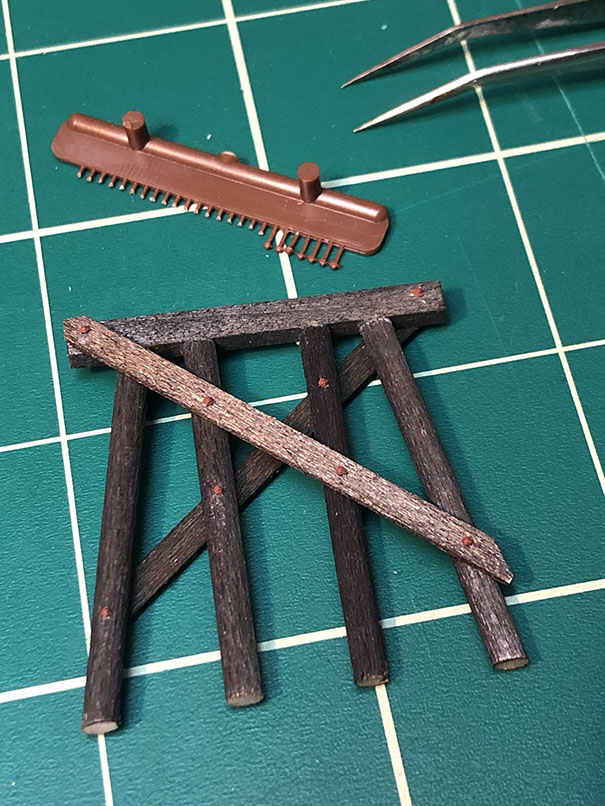
I knew there was a better way. A bit of brainstorming and Googling, I found the Dremel 220-01 Workstation, which is essentially an arbor press for your Dremel multitool. Using the Dremel 4486 Keyless Chuck with my #76 bit, this worked a treat. The Workstation was only $45 at Home Depot, which I think is a bit of a steal considering the excellent functionality of the tool.
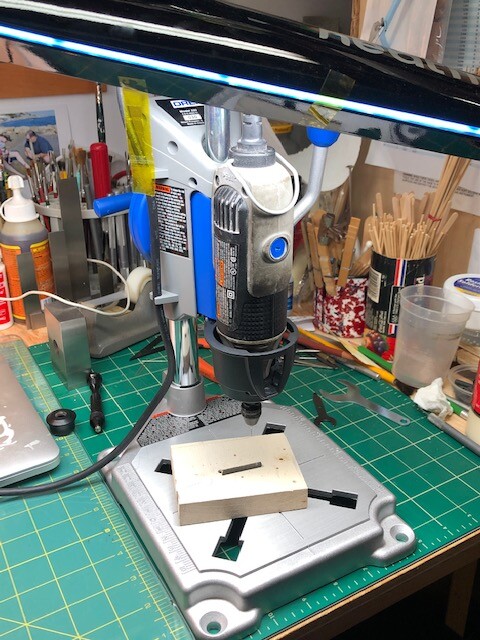
After assembling several bents, I decided to change gears and work on another part of the trestle – the deck. I needed a change of scenery. This required clearing down my workbench and developing a new workflow. I knew I wanted to assemble both sides at the same time. This would allow me to have everything aligned and placed on the same level, except for the center deck girder section which I’d have to spike in place later. Once both sides were spiked down, I could flip the whole rail and top deck over and glue the bents in place, upside-down. Again, this would allow everything to be aligned perfectly on the same plane. At least, this is the plan. I used an old shelf that I had in storage in the garage as a base. The shelf is straight and level and when I need to move it off my workbench I can do so easily.
I first used a straight edge to align and then tape down the plans on the board, side by side. I then used used some double-sided tape (which I had removed some of the tackiness from by touching my fingers to both sides) placed on the plans to secure the laminated stringers to the plans. (I previously laminated four sets of three 8″ x 16″ (HO scale) cut to length using a straight edge on a sheet of glass)
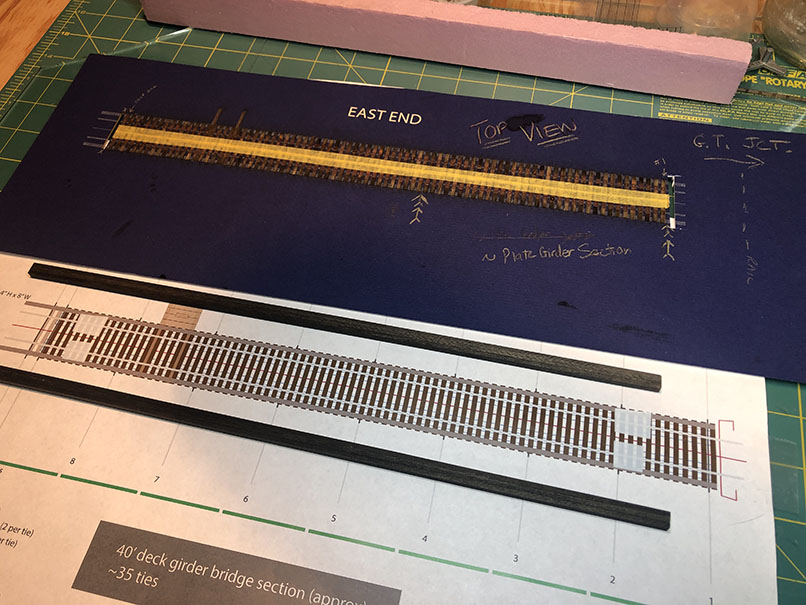
As you may recall, I had previously installed the ties into the laser-cut mat board jigs I made and installed Proto:87 tie plates. My plan was to put some glue on the bottom of the ties and then carefully place the jig/ties onto the stringers, weigh them down, and then once dry, lift the jig off of the glued-down ties.
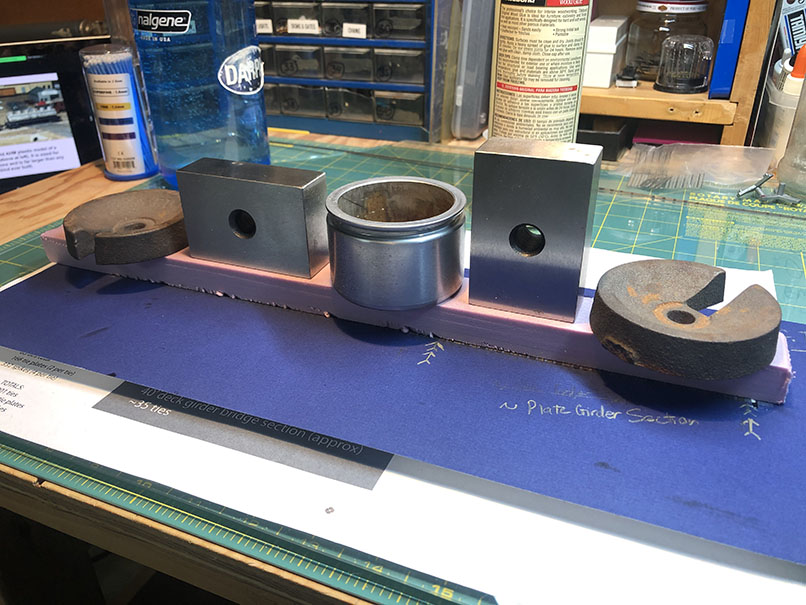
Well, this very much did not go as planned and resulted in the first big “disaster” of this project for me. When I began to remove the jig, ever-so-carefully, it began to “flake off” the scale tie plates and about 1/3 of the ties with it. Apparently the glue did not quite reach between the ties and the stringers (not enough) and the tie plates, well that was a mistake to begin with. They were never really aligned correctly and I should have never put them on first. In hindsight, this was a mistake. So now I had a mess to clean up.
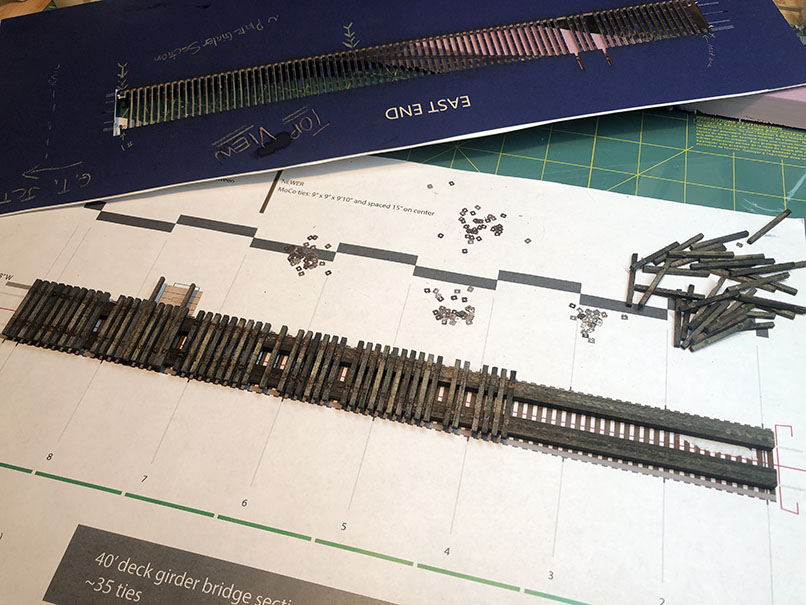
First, I picked off all of the old tie plates from the ties, sorted and stored them. I then removed any other loose ties. Next, I re-glued any of the wayward ties back in place, using my plans as a guide.
Gluing the ties Aligning the ties Weight while glue dries Picking off the previously installed Proto:87 tie plates
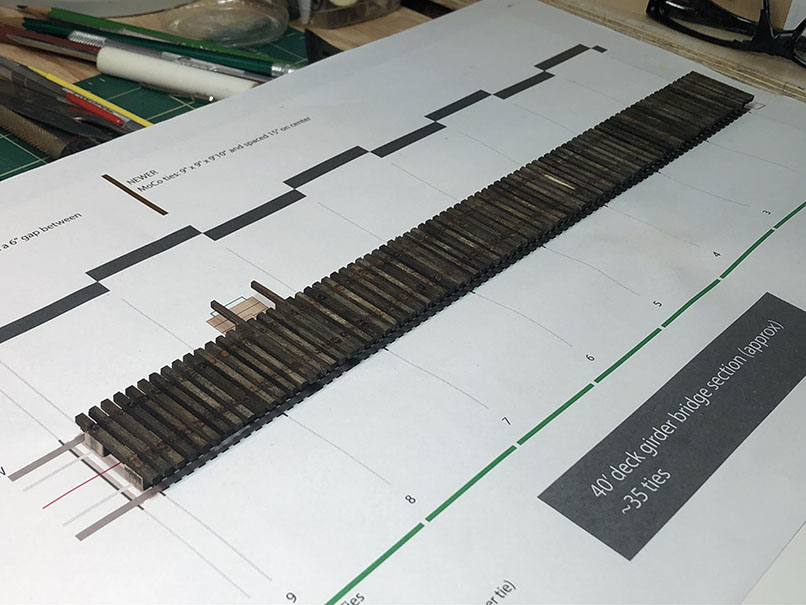
For the other side, I decide to be a bit smarter on the approach. I laid a strip of masking tape atop the ties in the jig and carefully, using a putty knife, pried the ties slowly out of the jig. This worked well. Once they were removed, I laid glue on the ties and placed them atop the stringers where I aligned them using the plans. I placed a piece of extruded foam and some weights atop the assembly to dry overnight. This worked well.
Prying up the ties Nearly done Stringers laid down on the plans Ties glued and placed on plans with weight Time to dry overnight.
Over the last few weeks (catching up to today) I have been working on installing the rails. I chose to use Micro Engineering’s 30-108 Micro Spikes and the Proto:87 tie plates. I am generally spiking the rails about every five ties, and the ties that have no spikes will get the tie plates. This is an incredibly tedious process but the end result will be some nicely detailed track. I experimented with installing the Proto:87 spikes, but decided I didn’t have the patience to go through with spiking all the tie plates so that’s where I’ll be drawing the line. Here are some photos of this process:
And so here is a photo from today:
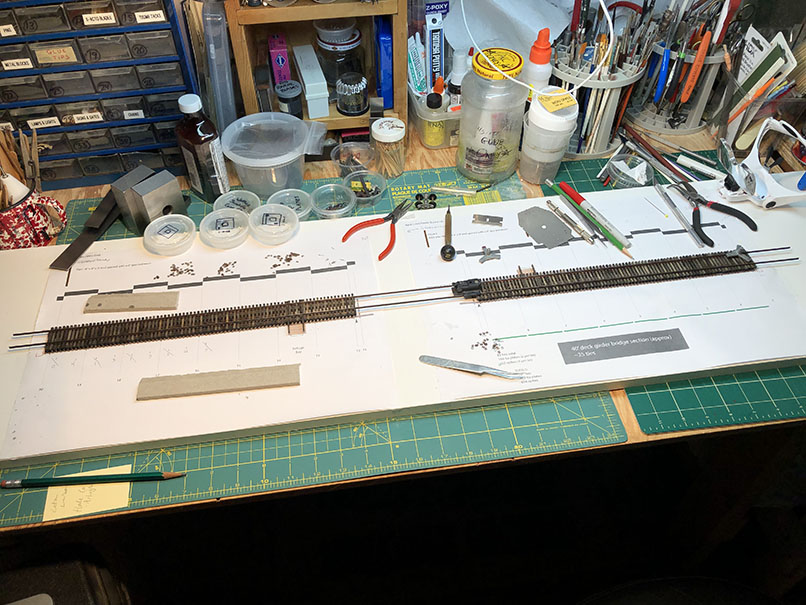
I’ve got three of the four rows of spikes done. The bottom right is the one I’m working on now. Once this is completed, I will set it aside and continue working on the trestle bents. Once they are done, they can begin to be installed. My aim is to have this completed by the end of the Summer, so hopefully you’ll be seeing an update sooner!
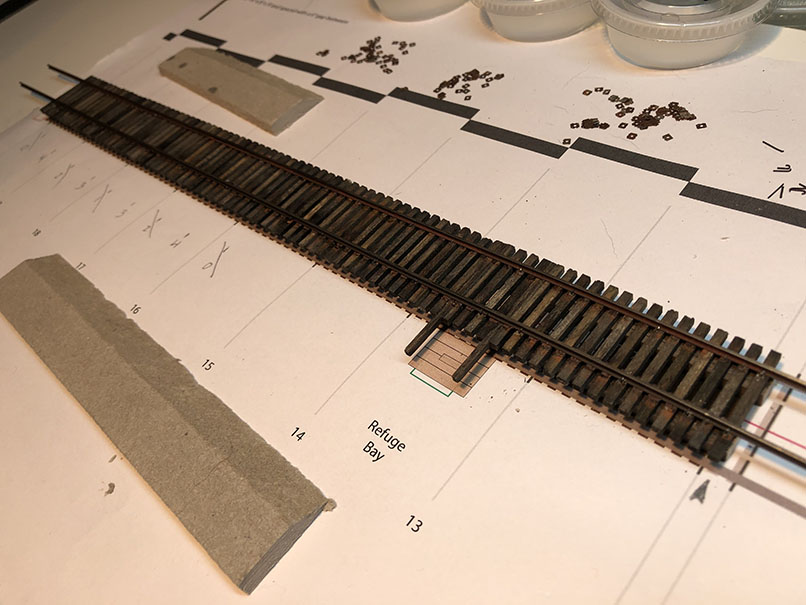
If you’ve got any questions or comments about the project, would love to hear them!